

Generate shop floor paperwork automatically, including standard parts lists and routing instructionsĭifferentiate work orders and rates by type, priority, and status Make real-time modifications to routing instructionsĭisplay quantity ordered, completed, and scrapped for each operationĬreate work orders and rates automatically from Material Requirements Planning (MRP) by answering action messages, or from sales order entry and select kits for assemble-to-order environments Modify the sequence and status of each operation on the routing Use master routings or non-standard routings for items and indicate when to use each itemĬhange the work centers and procedures for each operation on the routing
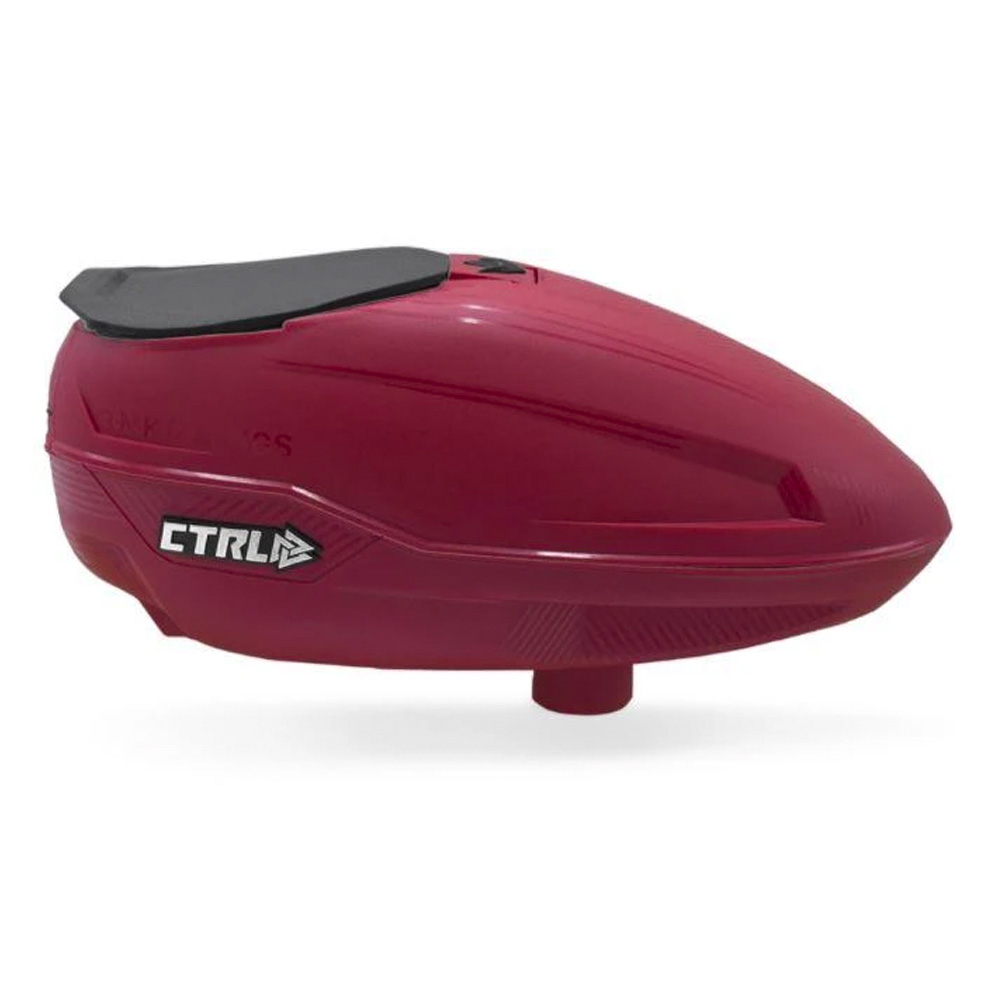
Generate a routing automatically when a work order is processed Review and analyze reports of work orders with detail by operation of standard versus actual for:Ĭharge actual hours and quantities to a work order as each manufacturing step is completed The Warehouse Management system allows you to originate picking requests through Manufacturing systems, which further enhances the automated method of tracking inventory movement within a warehouse.įigure 1-2 Shop Floor Control System Featuresĭescription of "Figure 1-2 Shop Floor Control System Features"Įnter and track time and quantities completed and scrapped by work order and by employeeĪllocate and track resource usage by work center per calendar month The Distribution Requirements Planning, Master Production Scheduling, and Material Requirements Planning systems provide suggested purchase and manufacturing orders required to maintain a valid production schedule. The Procurement system allows you to automatically generate purchase orders for subcontracted operations on your routings. You can record hours and quantities per work request or per employee to accommodate both piece-rate and hourly rate employees. The Payroll system interface allows single entry of employees' hours. This allows you to effectively manage the loads on your work centers to maximize production and meet scheduled demand. The Capacity Requirements Planning system reads the routings for work orders and rate schedules and monitors the load on the work centers involved. The Sales Order Management system allows you to generate work orders when you enter a sales order and updates sales information from within the Shop Floor Control system. You can perform inventory issues, commitments, and completions, and track order quantities throughout the production process. The Inventory Management system allows you to track materials between inventory or storage locations and the shop floor. The Product Data Management system provides information about bills of material, work centers, and routings. Description of "Figure 1-1 Shop Floor Control System"
